Утечка хладагента (фреона)
Чтобы камеры качественно охлаждались, хладагент должен быть в достаточном количестве. Если же происходит утечка вещества, снижается производительность холода, происходит чрезмерная нагрузка на компрессор, которая приводит к его поломке и дальнейшей замене.
Факторы, указывающие на наличии утечки хладагента:
▷ Техника не отключается, ее мотор работает постоянно, перерывов почти нет;
▷ Не холодит холодильник;
▷ В приборах с одним компрессором плохо морозит и холодильная, и морозильная камеры, в моделях с двумя компрессорами недостаточно охлаждается какое-то одно отделение;
▷ Вздувается задняя стенка камеры или на корпусе снаружи, так как утечка хладагента в холодильнике приводит к деформации материала;
▷ Могут появляться следы желтоватого оттенка на внутренних элементах камеры;
▷ Звуки, которые схожи с тем, что что-то булькает. Это объясняется попаданием в систему воздуха, который при смешивании с фреоном образует пузырьки;
▷ На дисплее появляются аварийные сигналы (сообщение о том, что имеет место сбой температурного режима);
▷ Температура конденсатора комнатная или он слегка теплый;
▷ Между камерами холодильника и в морозильной камере ржавчина, подтеки на уплотнителе дверцы рыжего окраса.
Этапы устранения утечки:
1.Обнаружение места вытекания газа. Специалист визуально осматривает электроприбор в поисках видимых «симптомов» — ржавчины или вздутия. Затем, используя течеискатель, который фиксирует концентрацию паров фреона в воздухе, находит точное место;
2.Нейтрализация утечки. Если место «доступное», в этом нет ничего сложного. Так, если место утечки — «теплый» контур, дефектный участок вырезается и система закольцовывается. А если хладагент выходит из запененной части, мастер выбирает наиболее безопасный способ ремонта;
3.Установка нового фильтра-осушителя. Этот элемент всегда заменяется, если происходит утечка, поэтому, когда мастер сообщает вам о его замене, он не пытается обмануть. Замена нужна для предотвращения попадания частиц влаги в контур охлаждения;
4.Проверка стопроцентной герметичности. Чтобы проверить степень герметизации системы, механик нагнетает в контур азот. Сверяясь с показателями манометра, мастер следит за давлением. Если тест успешен — газ стравливается, а ремонтник действует дальше по плану;
5.Вакуумирование. Чтобы вывести из контура воздух и влагу, берется специальное вакуумное оборудование. Его подключают, используя клапан Шредера, после чего идет откачка до достижения нужного уровня вакуума;
6.Перезаправка хладагента. Выходя на финишную прямую, мастер выбирает подходящий хладагент и производит заправку. Вводится он в систему также по клапану Шредера, после чего идет откачка фреона в контур из баллона. Уровень закачки газа определяется с ориентиром на требования изготовителя. Степень заправки контролируется манометром или с учетом массы — тогда баллон взвешивается.
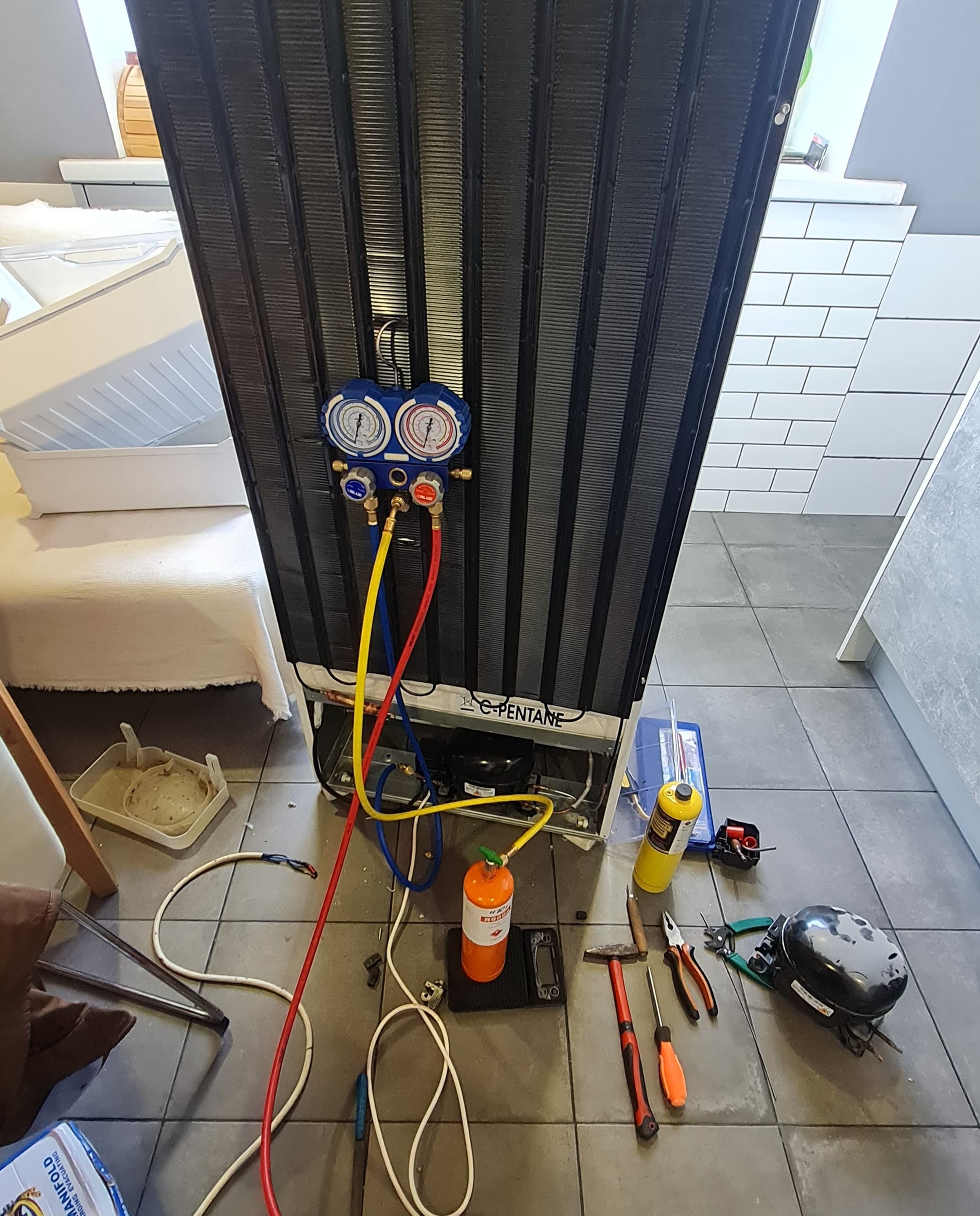